Brooklyn Park’s Ametek Mocon on ‘Cutting Edge’ of Sustainable Packaging Testing
Have you ever wondered how food products get their “best by” date? You may be surprised to learn that a company in the Twin Cities northwest suburbs is behind the answer.
Companies around the globe rely on Brooklyn Park-based Ametek Mocon to test packaging.
“We work with pretty much all of the biggest companies you can think of. From health care, pharma, med device, and food and beverage, you name it, we most likely work with them,” said Marc Coudeyre, marketing communications manager with Ametek Mocon.
Founded in 1966 by a General Mills scientist, Ametek Mocon is the global leader in packaging testing. The company predominantly focuses on testing packaging for food products, which is about 80 percent of its testing work.
“Water vapor makes them soggy, oxygen makes them not taste good. Potato chips are a perfect example,” explained Jeff Jackson, senior products manager at Ametek Mocon.
The company’s gas permeation testing laboratory is the largest of its kind in the world. The lab testing helps businesses meet expectations for product shelf life. It’s a tedious process. Getting results for various packaging films can take days, even weeks.
“As you can imagine, gas molecules don’t move through a barrier quickly,” Jackson explained.
Besides providing testing services, Ametek Mocon manufactures testing instruments that are shipped globally. Jackson said the company shipped out more than 400 instruments last year, a company record.
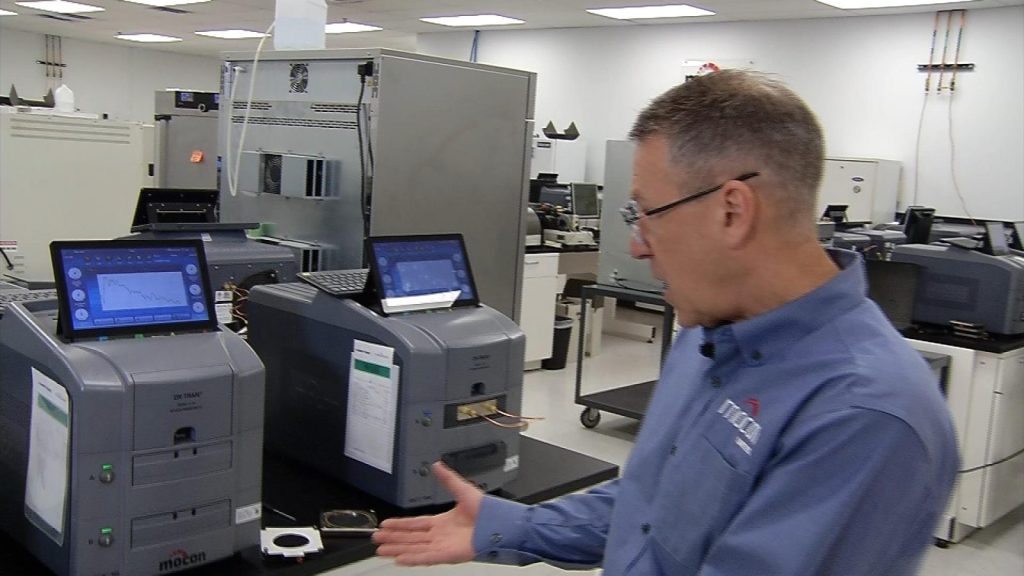
Jeff Jackson shows one of the instruments insides the permeation testing lab.
Ametek Mocon’s Increasing Sustainability Focus
With about 120 employees at its Brooklyn Park facility, work at Ametek Mocon is expected to get even busier. That’s because the packaging industry is rapidly evolving due to increasing attention toward sustainability and environmental stewardship.
“We are at that cutting edge of really being able to help our customer companies accomplish their sustainable goals,” said Coudeyre.
Ametek Mocon is working on new equipment that can test a range of new packaging, whether they’re made from recyclable materials or paper-based barriers.
“All the companies that are the brand owners themselves that want to advertise their environmentally friendly package, to their suppliers of the materials, to the people that actually make the raw materials, everyone of those we’re finding they’re developing new barrier materials, and they’re using our instruments to help develop those,” said Jackson.
Also See: Hennepin County Businesses Aim to Recycle 75% of Solid Waste by 2030